The global dilemma facing drivers today involves striking a delicate balance between the affordability of electric vehicle (EV) batteries and their ethical sourcing. With projections estimating a surge in EV sales to tens of millions by 2030, the demand for critical minerals like lithium, copper, and nickel is set to skyrocket. However, meeting this demand poses a significant challenge.
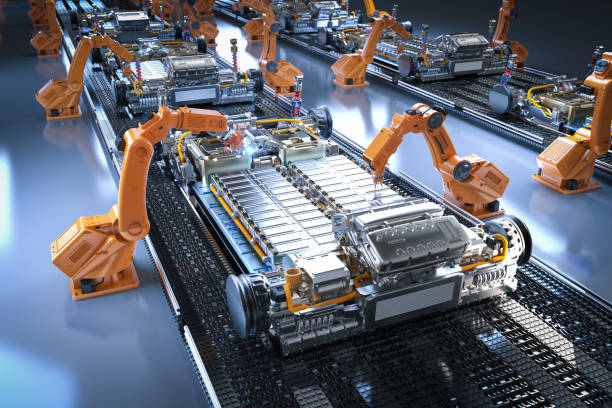
According to S&P Global, the market demand for lithium-ion batteries in light vehicles is expected to reach around 3.4 Terawatt hours (TWh) annually by 2030, while the current industry output is merely 0.30 TWh. Even if new lithium reserves were discovered, it takes 15 to 20 years to develop an operational mine from discovery. Moreover, there’s a notable lack of transparency in tracing the sourcing of battery metals.
While the industry has become adept at tracking emissions, the same cannot be said for monitoring ethical, social, and governance (ESG) violations, such as forced labor, within the EV battery supply chain.
To tackle this challenge, Bindiya Vakil, CEO and founder of Resilinc, a supply chain risk management specialist, emphasizes the crucial role of artificial intelligence (AI) in achieving supply chain visibility. She suggests that autonomous AI mapping and supplier-validated mapping are vital tools for gaining deep insights into multi-tier supply networks. This is particularly important in identifying high-risk regions and sanctioned suppliers, allowing manufacturers to find alternative compliant sources.
The introduction of regulations such as the Uyghur Forced Labor Prevention Act (UFLPA) and Corporate Sustainability Due Diligence (CSDDD) is pushing the industry to address ESG risks, including forced labor. Vakil stresses the need for assessments, ESG evaluations, and custom compliance assessments to establish direct communication with suppliers. This collaborative approach not only fosters transparency but also provides an effective means of addressing concerns and violations.
In the EV battery supply chain, shining a light on vulnerable suppliers is crucial. Assessment scores help quantify supplier compliance, allowing automakers to prioritize addressing forced labor risks in sub-tier levels. Vakil suggests joint plans with suppliers that include worker training, remediation plans for identified violations, and sanctions for non-compliance.
Active supplier monitoring is emphasized as a key element in maintaining a clean EV supply chain. Tracking the progress of implemented mitigation plans ensures long-term compliance and reduces forced-labor risks. Consistent communication and collaboration are deemed fundamental in achieving these goals. As the EV industry rapidly evolves, a proactive and transparent approach to supply chain management is essential for sustainable and ethical growth.